Introduction to bus bar
Busbars are key components in power distribution systems and are conductive pathways that facilitate efficient transmission of electric current. While copper has long been the traditional choice for busbars due to its excellent conductivity and mechanical properties, the question remains: does the busbar have to be copper? This article will explore the various materials used for busbars, the pros and cons of copper, and alternative materials that can be effectively utilized in different applications.
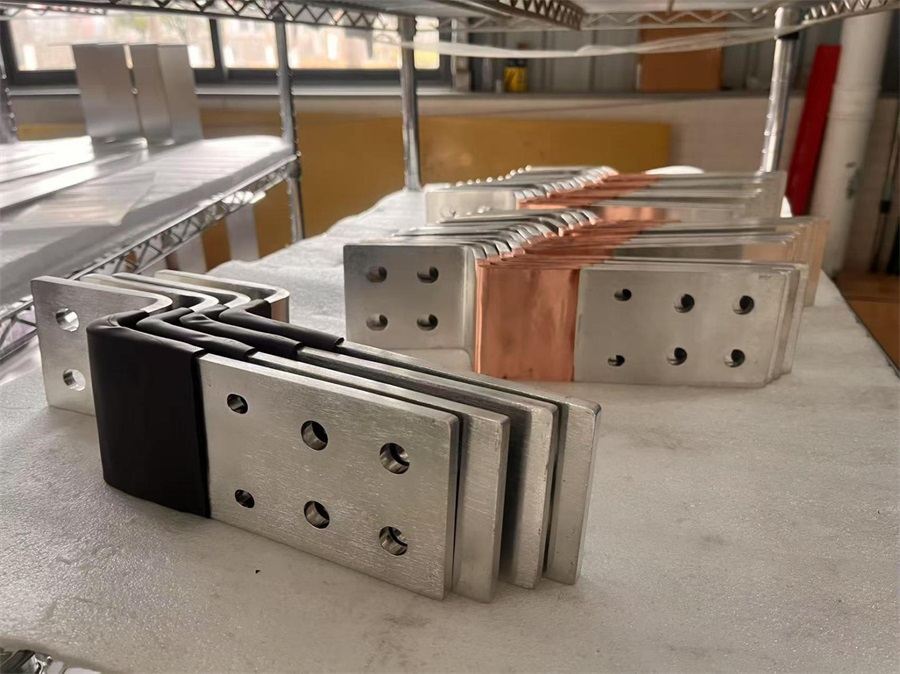
Copper busbar case
Excellent electrical conductivity
Copper is known for its high electrical conductivity, about 59.6 x 10^6 S/m. This property enables copper busbars to carry high currents with minimal energy loss, making them ideal for high-performance applications. Copper’s superior conductivity ensures electrical systems operate efficiently, reducing the risk of overheating and wasted energy.
Corrosion resistance
Another significant benefit of copper is its natural resistance to corrosion. This feature increases the durability and service life of the copper busbar, especially in environments where moisture or corrosive substances are present. Copper’s corrosion resistance helps maintain the integrity of the electrical connection, ensuring long-term reliable performance.
Mechanical Strength
Copper also has excellent mechanical strength, allowing it to withstand pressure and strain without deforming. This feature is particularly important in applications where the busbar may be subject to vibration or thermal expansion. The mechanical strength of copper busbars contributes to their reliability and safety in various electrical systems.
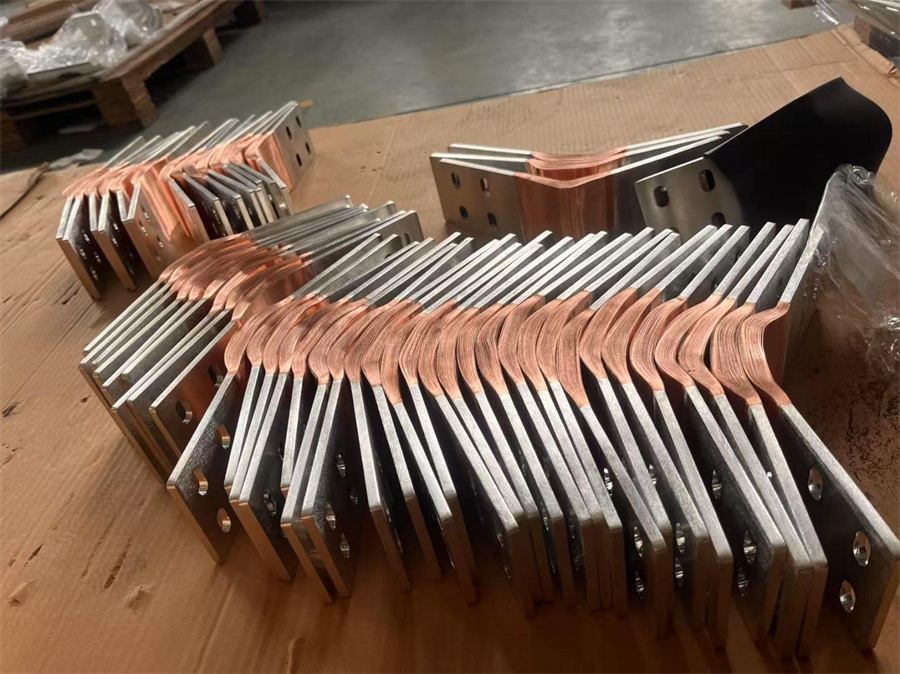
Alternative materials for busbars
aluminum
While copper is a popular choice, aluminum is increasingly being used as an alternative material for busbars. Aluminum has an electrical conductivity of approximately 37.7 x 10^6 S/m, which is lower than copper but still sufficient for many applications.
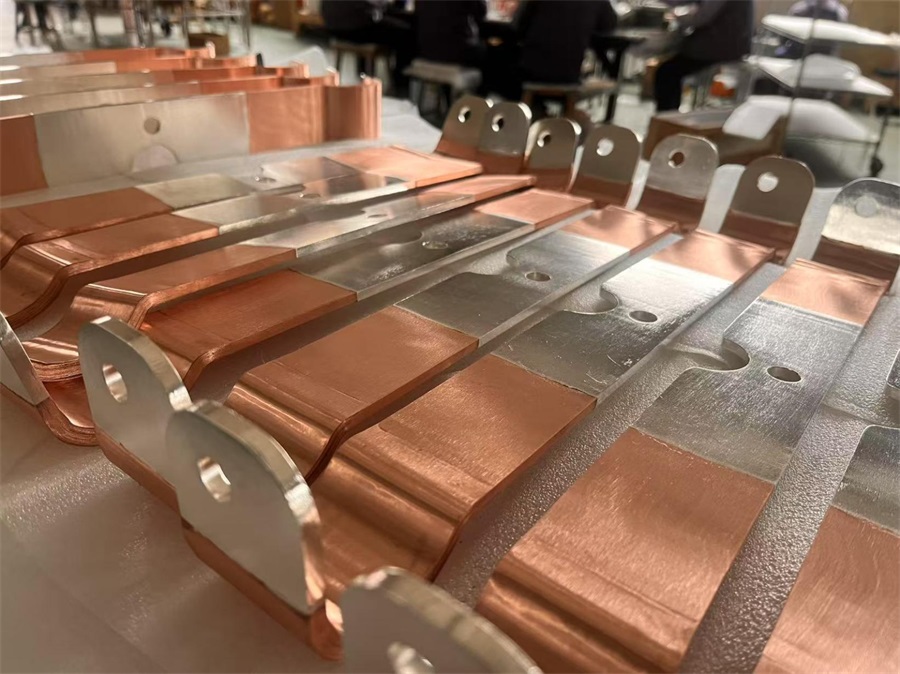
Advantages of aluminum busbar
Lightweight: Aluminum is much lighter than copper, making it easier to handle and install. This feature is particularly useful in weight-sensitive applications, such as electric vehicles and aerospace.
Cost-effective: Generally speaking, aluminum busbars are cheaper than copper, making them a more affordable option for many projects.
Sufficient conductivity: Although aluminum has a low conductivity, it can still carry large amounts of current efficiently, especially when designed with a large cross-sectional area.
Copper alloy busbar
Copper alloys such as brass or bronze are sometimes used for busbars to combine the advantages of copper with its enhanced mechanical properties. These alloys can provide increased strength and wear resistance, making them suitable for specific applications.
Advantages of copper alloy busbar
Increased Strength: Copper alloys can provide higher mechanical strength than pure copper, making them suitable for high-stress environments.
Corrosion resistance: Many copper alloys have excellent corrosion resistance, which can extend the service life of the busbar under harsh conditions.
Other Materials
In addition to copper and aluminum, busbars are also made of other materials such as stainless steel and composite materials in specialized applications.
Stainless steel busbar
Stainless steel has good corrosion resistance and mechanical strength, suitable for environments where both properties are required. However, its conductivity is lower than that of copper and aluminum, which may limit its use in high-current applications.
Composite busbar
Composite materials, which may include a combination of metal and insulating materials, are also being explored for busbar applications. These materials can provide unique properties such as lightweight structures and enhanced thermal management.
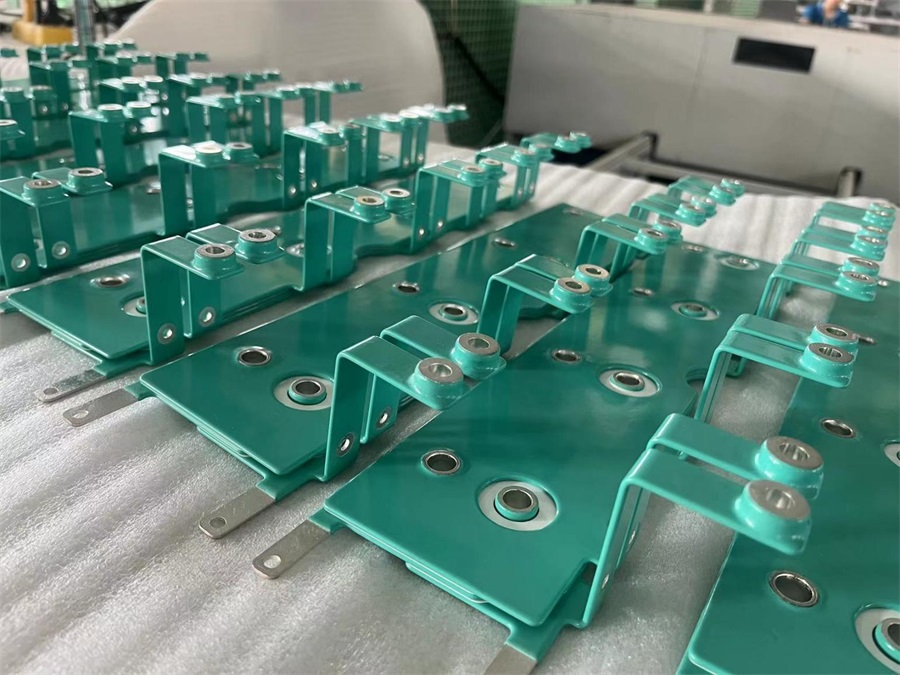
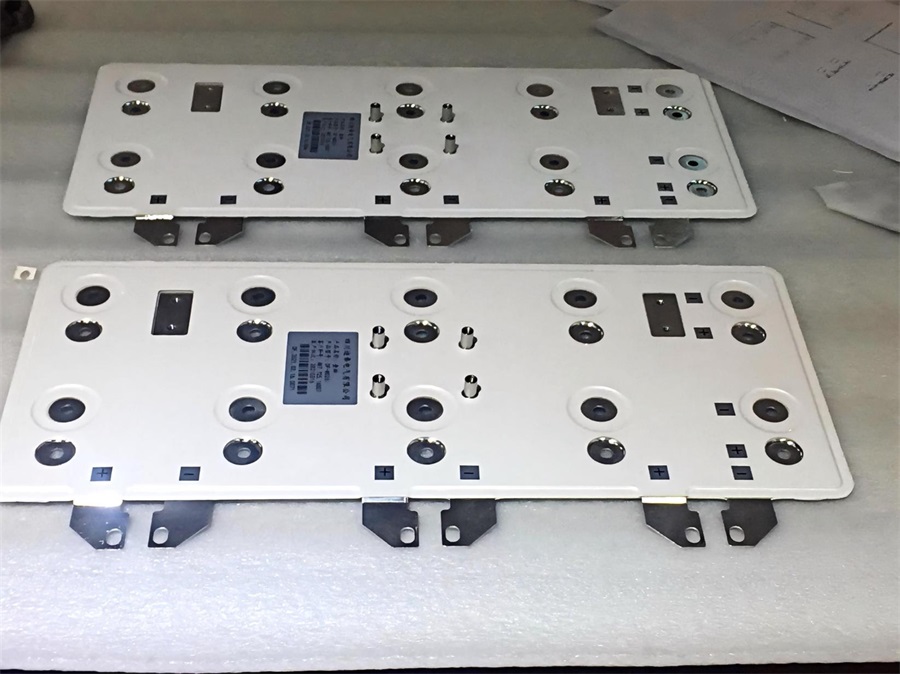
Factors affecting material selection
When deciding whether copper is necessary for busbars, several factors must be considered:
1. Current carrying capacity
The conductivity of a material directly affects its ability to carry electrical current. For applications with higher current demands, more conductive materials such as copper are preferred. However, aluminum can also be a viable alternative if designed properly.
2. Environmental conditions
The operating environment is critical to the choice of materials. If the busbars will be exposed to moisture or corrosive substances, materials with high corrosion resistance, such as copper or certain alloys, are ideal.
3. Weight and space restrictions
In applications where weight is a concern, such as transportation or aerospace, aluminum busbars may be favored for their light weight.
4. Cost Considerations
Budgetary constraints can significantly influence material selection. While copper has excellent properties, aluminum may be a more cost-effective solution for some applications.
in conclusion
In summary, while copper is an efficient and traditional choice for busbars due to its excellent conductivity, corrosion resistance, and mechanical strength, it is not the only option. Aluminum, copper alloys, stainless steel and composite materials may also be viable alternatives, depending on the specific requirements of the application. Understanding the advantages and limitations of each material is critical to making informed decisions to improve the efficiency and reliability of power distribution systems. Ultimately, busbar material selection should be based on a careful evaluation of application requirements, environmental conditions, and budgetary considerations.
Post time: Feb-21-2025